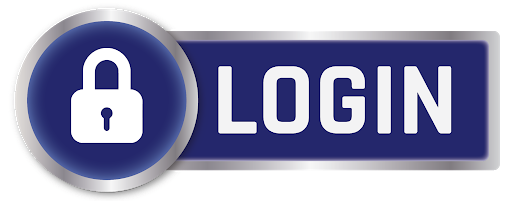
The Key Features Of Wifi ACC :
- Key Feature # 1-Soft Start : When first powering up AC induction motors are like a long piece of copper wire – i.e. they act more like an “electric short” than an “electromotive machine”. A huge motor current in-rush many times greater than motor full load current occurs with AC motors. The ACC using OP based techniques limits /lessens motor power-up current to only as much as needed to get the motor moving, which is often much less current than the full load current, then gently / softly intelligently adjusts or adapts the motor to its actual operating speed. Motor start current is “softened” substantially or “greatly reduced” vs. the “standard or normal” AC motor start current.
- Key Feature # 2-Demand Power Reduction : As noted above in the soft-start feature this ACC ability to greatly reduce start-up current also provides a significant reduction in energy and costs commonly known as “kw demand.” These are actual extra fees charged by Utility Companies because of the added costs associated with providing extra grid or system capacity to handle the excess power needed to accommodate AC motor start-up. Picture the thousands if not millions of motors powering up every morning each consuming up to four (4) times what it needs normally. This “demands so much excess power” in the same time frame that incentives are given by the Utilities to stagger the start times for many electric users …. This “Demand Problem” is eliminated with the ACC (=ACC)..!!!…
- Key Feature # 3-Anti-Stall : Many AC motors have loads that are not always consistent or static, these loads may and often do change. Even if the motor load doesn’t change the input voltage / power to the motor does. In fact the electric grid to which motors are connected can vary significantly many times throughout the day. To overcome this variability and avoid stalling, most motors are designed to provide more power than usually needed. Slowing a motor down using a variable speed controller cuts down the power to the motor as power is a function of motor speed times motor torque, but this can make the motor even more susceptible to the variations mentioned above.
- Key Feature # 4-Brown-Out Ride-Thru & Recovery : Brown-out is a term often heard more in the summer months and it refers to a condition of the Utility Company’s electric power grid. When the power demands on the electric grid exceed the power available from it the grid’s power delivery drops. This lower power level means that all the loads, machines and systems connected to the grid have less power than they require. This will cause lights to dim (brown), motors to run slower and drives them or causes them to work harder, run hotter and draw even more power. These increasing stresses to the grid can have a downward power spiral effect “lowering, dimming or browning” the grid power to the point of a blackout –i.e. no power is left on the grid. If the “in-between” brownout condition remains for any length of time this can severely damage motors and machines to the point of “burnout”. The ACC again has the OP based intelligence to recognize this threat condition and will then “adapt the power to the motor” to minimize the brownout effects and can actually protect and save the motor from burnout due to brownouts!
- Key Feature # 5-Adaptive vs Variable Speed : Many motor controllers tout “variable speed” operation when in point of fact they are only multi-speed; ie they do not continuously and smoothly vary speed throughout an operating range. These have instead a series of “fixed motor steps or speeds” that cannot settle in between or at the optimum speed for the current need. For instance in a fan operation there may be up to 3 or 4 preset speeds (=airflows), but the climate conditions at the moment prefer 650 cfm of airflow; but there is either 800 cfm or 400 cfm as the “step / variable speed” option. Now the choice is either too much air or not enough for the conditions preferred. The ACC is truly not just “variable speed” (i.e. it has continuous smooth full range) it uniquely has “adaptive speed”. For instance it can provide the above 400 cfm or 800 cfm, as do other competing units, but the ACC can also provide any speed (airflow) inbetween; so if conditions call for or need 650 cfm, 525 cfm or any thing else the ACC will intelligently and dynamically adjust to that optimum speed need. And if conditions change, when conditions change real time, unlike competing digital systems and Electronically Commutated Motors (ECMs) that “presume a fixed airflow profile” the ACC OP based unit “Adapts to the Real Time, Real World airflow needs.”
- Key Feature # 6-Idle Speed : This was / is another ACC first that is a real plus and patented feature. Most conventional and competing units turn the fan off once climate conditions (set point)appear met. The ACC instead of shutting off throttles back energy and airflow to a very low speed, quiescent level airflow or “idle speed”. This allows for a gentle but continuous air movement that helps keep equilibrium of climate conditions in the occupied space. Rather than static stationary air that creates hot and cold spots along with poorer air quality the ACC improves the indoor air climate, comfort and quality. Also remember the energy impact that starting and stopping AC motors causes (see 2-above). By not starting and stopping the motor saves motor demand energy, lessens motor and system stresses and reduces air noise. Just as it really is not practical or sensible to shut off your car motor at every stop light but instead let it idle then gradually add power / speed as needed, so does the ACC to fan motors.
- Key Feature # 7-Energy Efficiency : The value of variable speed on AC motors has long been pursued primarily to achieve energy savings. It is well known in the HVAC Industry and many others also that slowing a motor down reduces the power the motor is consuming. When this is done with a fan the savings become even more dramatic… For instance if the speed of a motor running a fan is cut to 50% of full speed the power is cut by over 75% ! Often the load, machine, system or unit that the motor is operating does not require or always need full power. As an example in several installations using an HVAC fan coil it was determined that only 15% of the on time was it necessary for the fan to be at full speed …85% of the time only low to very low speed was needed! Yet without variable speed there are only two choices full power or no power. So most motors flip between on or off –i.e. full power or no power. Any variable speed system that can go “in between these two extremes” should and usually does save energy; but some do this better than others and many do this with more or less harm to the motors, machines, loads, AC grid and even nearby unconnected systems. Energy savings achieved with the ACCUnit are throughout the entire operating range and generally save from 20% to over 40% of the energy the same system uses in its standard operating mode. This is not only much greater than competing systems, but the OP based methods used by the ACC also saves this energy in a “clean way” without many of the harmful electrical noise effects caused by other digital based units (see 10 below).
- Key Feature # 8-Temperature Tracking and Control: One of the main components of the ACC Unit’s many features is real time system output temperature tracking and resultant motor fan speed control. The ACC is capable of monitoring temperature and adapting fan speed for changes detected in system output air, heat or cool.But the ACC does more than just output a fixed airflow to temperature line as most others do; it “ tracks and adapts the airflow to heat (or cool) available”! A unique patent pending profiling technique is used to provide a nonlinear but adaptable thermal content vs just temperature level airflow tracking. Most systems wait until the plenum or coil is well into its heating or cooling cycle before turning on the fan motor to full speed, and then turning off well before all the heat or cool available has been utilized. With the ACC the fan motor is always at idle until the temperature sensors detect a change that will increase fan speed proportional to the heating or cooling available to be distributed into the occupied space. What this means to you is ; quicker and more uniform distribution of desired air, total usage of heat and cooling generated in your system, or more simply stated comfort and savings.
- Key Feature # 9-Direct Sensor Input and Control: As mentioned above the temperature tracking and control is a direct result of sensor input and control. Currently temperature and remote building control systems are the two main inputs to the ACC that will result in fan motor speed control. These sensor and control inputs will cover the majority of retrofit and OEM market applications currently being installed. Sensor or control inputs take the guesswork out of the old manual speed adjustment systems, once properly installed the ACC will take control and eliminate the necessity of constant manual speed changes. There are several other sensor inputs, such as; humidity, pressure, rpm, and remote control inputs that are in development, which will, when properly installed, result in the best possible comfort levels and energy efficiency for your application. If these utilize standard electrical parameters (i.e. volt, current, resistance) then the ACC can interface to them.
- Key Feature # 10-Analog vs Digital PWM Inverters for Motors: Most motors are analog yet most controllers that power them are digital and try to force the motor to accept digital power known as PWM or Pulse Width Modulated power. This type of switched power is NOT motor friendly, especially to AC motors. PWM creates electrical noise, harmonics and stresses in other electrically powered systems and devices nearby or also connected to the same power grid. The ACC is a lot more motor friendly and also avoids creating many of the other noise and stress problems found in other variable speed drives and units.
Top